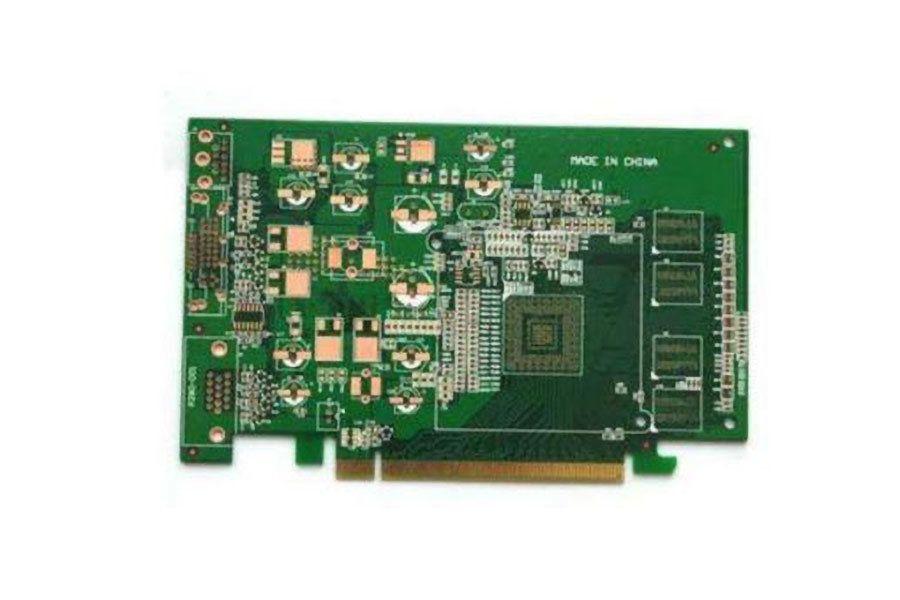
What is a Flexible Printed Circuit Board?
Flex PCB’s are patterns of conductive traces on flexible substrates, or a more precise description is – flexible circuitry for your next best product. Flex Circuits have been in use for some time now but are being utilized far more in everyday products as designs become more compact and complex.
So, what is a flexible printed circuit board really? We all have seen many examples of rigid PCBs and recognize that more and more electronics are being used in everyday products and devices. More electronics need more interconnectivity, which rigid PCB's cannot provide in the form factor of many of these devices.
That is where flexible printed circuit boards provide the solution. The electronic design has become very demanding of size and shape, and flex PCBs can bend, fold and be configured to fit into space as required. Variable thickness and substrates have also made the use of rigid PCBs almost obsolete. With componentry getting smaller as technology develops the use of flex PCBs in products has grown significantly.
Flexible printed circuit boards are made up of 2 main parts – conductive traces and substrate – mostly the conductive trace is copper which is then protected by the substrate which is either polyimide or a solder mask. The use of polyimide is because is offers excellent insolation and is flexible with high resistance to contamination and high temperatures.
Flex PCB's can be printed in single, double or multi-layered configurations depending on the design specification.
- Single Layer – a single layer of conductive traces on one side of the substrate – 1 circuit
- Double Layer – a single layer of conductive traces on both sides of the substrate – 2 circuits
- Multiple Layer – several layers of conductive traces on the substrate all separated by insolating material – multiple circuits
Depending on the design specifications for your product there are many combinations of trace/substrate that can be used for your flexible printed circuit board. Factors like temperature, mechanical use, chemical, current, and capacitance all have an influence on the manufacturing process. The most common manufacturing process used today is where the traces are printed or “cut out of a solid sheet and these traces then are imaged or screen printed on to the substrate. This is called the subtractive method. The additive process is the opposite where the traces are printed or plated on to the substrate where needed.
The subtractive method offers the most flexibility and is more robust which allows for more design configurations in your product. The additive process is used for very low current circuitry and this process has less environmental resistance.
Flexible Printed Circuit Boards offer a far wider choice in product design and production, making 3D designs and complex configurations a reality.