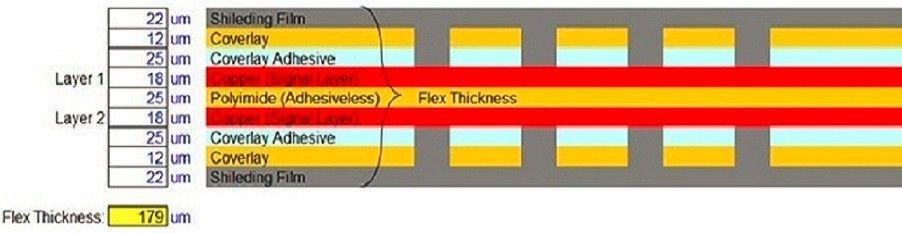
Flex PCB EMI Shielding Design
Designing a Flex PCB is as much a mechanical task as it is an electrical one. And balancing the two can sometimes become challenging. Another element of Flex designing that might crop up (especially in certain Flex applications) is the EMI shielding of the circuit. So in this article, we will try and cover what EMI shielding is, how its absence or presence affects a flexible circuit, and the different types of EMI shielding available for Flex PCB.
EMI Shielding of a Flex PCB
EMI – Electromagnetic Interference is the impact that electromagnetic waves have on a circuit. In most cases, it's the adverse side effect of the electromagnetic waves present in the vicinity of the circuit. In very few cases, EMI is induced intentionally to attack (or test the possibility of an attack on) a circuit’s functionality. EMI is also referred to as RFI (Radio Frequency Interference) when the frequency of interfering signals falls inside a specific range.
Why is flex pcb EMI Shielding Important
EMI has the potential to disrupt, and in extreme cases, halt the operation of a circuit. A lot of very critical-in-nature electronic appliances are susceptible to EMI disruptions. Devices like medical equipment (especially MRIs), military (drones and radars, etc.), aerospace electronics, and cell phones. EMI shielding is essential to prevent these appliances and circuits (many of which are either Flex or Rigid-Flex in nature) from the negative impact of EMI.
A number of sources can be responsible for the presence of EMI near circuits and appliances. Electrical trains, transmission lines, MRIs, electric motors, transformers, and ultrasonic pest control devices, etc. Distance matters when it comes to EMI and its sources. So a circuit may be affected more when it's near a source that is generating EMI, like an electrical transformer.
It is important to understand that an EMI shielding is essential for a flexible circuit to both prevent it from absorbing and radiating EMI. So proper EMI shielding is crucial in circuits because it not only ensures the proper unimpeded operation of the circuit itself, but it also prevents the circuit from disrupting the operation of other circuits or other parts of the same circuit with the EMI it’s causing.
This is especially apparent in the designing and manufacturing of Flex circuits for MRIs and cell phones. The magnetic operation of an MRI introduces a lot of EMI in its vicinity. Funnily enough, the sensors in an MRI are super sensitive to EMI, and the results can be disturbed by even the slightest introduction of stray magnetism in the vicinity of these sensors. So in an MRI, EMI shielding acts to prevent parts of the circuits from radiating adverse electromagnetic waves as well as other Flex PCBs in the vicinity from absorbing any EMI.
Flex pcb EMI Shielding Design
The job of an EMI shielding is to capture any stray electromagnetic radiation and dissipate it so that it doesn’t cause any problems in the operation of a Flex PCB and prevent any noises. So primarily, EMI shielding is a conductive layer that can capture and disperse EMI. The dispersion happens thanks to the EMI shield’s connection with the ground layer.
So the primary design considerations for an EMI shield are:
- A conductive layer
- Electrically connected to ground
But it’s not as easy when you are working with a Flex PCB. You have to consider the mechanical implications of adding another layer to the Flex PCB, especially if it’s a dynamic flex that has to be bent repeatedly. If the EMI shielding layer is too thick or relatively stiff in nature, it will limit the bending capability of a Flex PCB. Also, the EMI shielding layer is connected to the ground layer by openings in the cover-lay or cross-stitching of vias. Both of which further impact the flexibility of the Flex PCB.
One more consideration is the controlled impedance of some Flex PCBs. When impedance control is required in a Flex PCB (Cell phones), the EMI shield has to act as a control plane to achieve the necessary controlled impedance values. So other EMI shielding design considerations are:
- The flexibility of the Flex PCB.
- Impedance control of the circuit
Four Common flex pcb EMI Shielding Designs
There are four common EMI shielding practices prevalent the PCB designing.
- Silver ink
- Copper layer
- Crosshatched copper
- Shielding films (Thermoplastics)
1. Silver Ink
A layer of liquid silver (silver paste/silver ink) is applied (most commonly using the silk screening method) to the cover-lay of the Flex PCB. Openings are made on the outside edges of the cover-lay where the liquid silver flows in and establishes an electrical connection to the copper ground or signal layer for EMI dissipation. An additional cover-lay layer achieves the electrical isolation of the silver EMI shielding.
The method is cost-effective, relatively easy to fabricate and provides adequate EMI shielding. But it doesn't provide the requisite impedance control, and the addition of cover-lay layers adds to the thickness of the Flex PCB, limiting its flexibility.
2. Copper Layer
Simply adding a copper layer to the Flex PCB over the Polyimide layer(s) will result in the effective dissipation of the EMI. Stitched vias are used to connect the copper-based shielding with the ground layer.
This method provides the best EMI dissipation functionality as well as superior impedance control. But it restrains the flexibility of the circuit more than any other method.
3. Cross Hatched Copper
Crosshatched copper is mechanically superior to applying a simple copper layer. But its impedance control and dissipation capabilities are relatively limited compared to a plain copper layer.
4. Shielding Films
This EMI shielding method was introduced mostly owing to the needs of the cell phone industry, where battery-based EMI is a prevalent issue. The shielding films have a three-layer makeup: Friction-less black insulation layer, metallic disposition layer, and an electrically conductive adhesive layer. The shielding film is pasted on the Flex PCB using heat and pressure. The PCB’s cover-lay is opened up in specific places, where the conductive adhesive layer flows in (after being melted by the heat) and establishes the electrical connection with the ground layer.
Shielding films provide amazing shielding properties and have the best mechanical properties compared to other methods. It’s also the thinnest EMI shielding solution. Its impedance control is (in some cases) almost on par with a copper layer shielding.
Conclusion
EMI shielding is something many designers tend to overlook. This can have dire consequences for the dimensional and mechanical flexibility of your Flex PCB. The process can get much easier if you work with the leading Flex PCB fabricators. Companies like these have enough experience backing their manufacturing techniques and choice of material to cope with any design requirements you might have. They will also be able to advise you on the best designing techniques to get the most out of your Flex PCB, by recommendations like which type of EMI shielding design to go with. This simple choice can transform the electrical and mechanical performance of your Flex PCB.