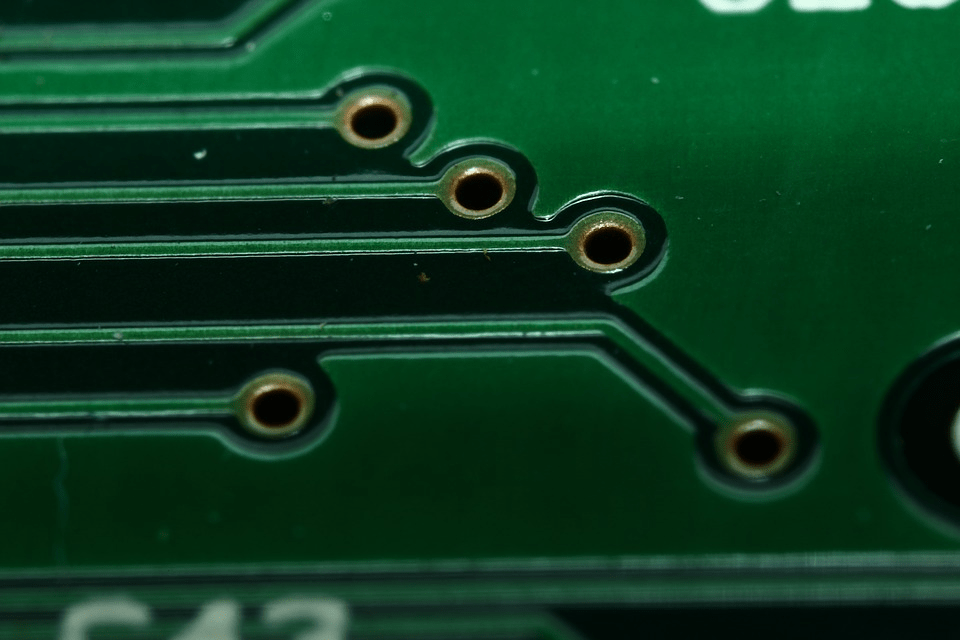
Common Material Stack Ups for Flex PCB
To assure that the delivered parts meet all of the design specifications for the client, any flex PCB design requires a comprehensive and correct PCB stack-up as part of their associated documentation. Preserving the accuracy of this information helps to minimize technical queries and delays in the supply of the products.
Material stack-ups for flex circuits are a graphical side angle view of the board that is often integrated into the mechanical layout in DXF, PDF, or Gerber format. The manufacturer needs the material stack-up to guarantee that the finished product is fabricated in accordance with all client specifications and that it meets the design's electrical requirements and mechanical bend.
The Importance of a flex pcb Stack-Up
The stack-up includes a substantial amount of data. It specifies the types of material to be utilized, their placements within the structure, the thicknesses of specific material layers, material item number if needed, and the overall thickness of the structure.
Multiple sections with different designs lead to multiple thickness needs in most flex circuit designs. Some regions might have a thickness that is crucial to the component's performance, such as bending requirements, impedance values, or connector specifications.
The stack-up also describes the essential construction features required for meeting IPC 2223C design criteria and verify the validity of the finished components for flex PCB designs.
Material flex pcb Stack-Up Construction
Polyimide film, copper, and an adhesive compound are all laminated or glued together using pressure and heat in flex PCBs. For increased flexibility, the copper employed is in the style of foil.
The non-conductive layer that covers the copper is made of polyimide film, which is pliable but incredibly durable, allowing it to endure the pressure and heat of the lamination procedure as well as the conditions of the ultimate device application. Next, the adhesive layer is applied to secure the surfaces together.
Even though acrylic is commonly used as an adhesive, it can present production issues in some designs, such as compressing into copper sections, which can cause electrical issues, and moisture out gassing, which can cause debonding or delamination. As a result, non-acrylic and adhesive-free solutions are also available.
In the lamination process, it's critical to use the right materials and thicknesses. An inaccurate stack up can result in flaws, delamination, and, in certain situations, even explosion. Your fabricator will have a variety of materials and thicknesses to choose from and can advise you on the best possibilities for your design.
Common Stack-Ups in Flex pcb
There are four different types of material stack-ups used in flex PCB. These are:
1. 1-Layer Flex pcb or Single-Sided Flex Circuit
One conductive layer of copper is positioned between the outermost layers of polyimide material in single-layer, single-sided flex circuits. A flex PCB in this configuration is the most basic. A common construction combining a Dupont base material featuring a cover-coat after an acrylic polyimide film copper overlay is used in some circumstances.
2. 2-Layer Flex pcb or Double-Sided Flex Circuit
Double-sided or 2-layer flex PCBs have two copper conductive layers with a polyimide layer in the center, layered with acrylic to connect the cover-coat outer layers. A conventional acrylic-based polyimide film copper-clad construction employing Dupont base components with cover-coat is used in this case.
3. Multi-Layer Flex pcb or All-Flex Circuit
The more layers you include in your flex PCB design, the more complex it becomes, and there are higher chances of problems arising.
Multilayer flex PCBs have three or even more conductive copper layers with polyimide layers in the center, placed between two layers of layer cover-coat bonded together with acrylic. A typical 6-layer structure for an acrylic polyimide film copper-clad employing Dupont-base materials including a cover-coat is commonly used.
4. 4-Layer Flex pcb or Rigid-Flex Circuit
As the name implies, rigid-flex PCBs have both flexible and inflexible portions. The stacking is significantly more difficult and requires the use of a different sort of bonding substance in addition to the acrylic adhesive. A basic loose-leaf construction employing Dupont base materials and rigid sectional bonding materials such as Epoxy no-flow pre-preg or polyimide is commonly used.
Complex flex pcb Stack-Ups
To enable a complete and well-defined specification of a complex flex design with many extensions, the material stack-up may need to be separated into zones. Attempting to specify the part in a single stack-up results in parts of different structures overlapping and altering the design's graphical depiction. The portion outline is then used to identify the specific sections.
When choosing a manufacturer, you should look for one that offers adhesiveless bonding choices. Non-acrylic and adhesiveless solutions should be considered as well because traditional acrylic adhesives may produce manufacturing issues for particular designs, such as squeezing into copper sections, causing electrical problems, or moisture out gassing, causing debonding or delamination.
Conclusion
Flex PCB manufacturing is becoming a popular design solution both for sophisticated, three-dimensional product manufacturing and advanced component surface mounting standards as a result of how much the portable communications industry has evolved throughout the last couple of years.
To meet the industry's needs, Hemeixinpcb offers fabrication of its core HDI technological advances in tandem with flexible PCBs. Hemeixinpcb can provide rigid-flex and flexible PCBs and HDIs for applications that require highly reliable circuits. To get a quote for your flex pcb design, you can click here. Alternatively, you can contact us for expert advice.