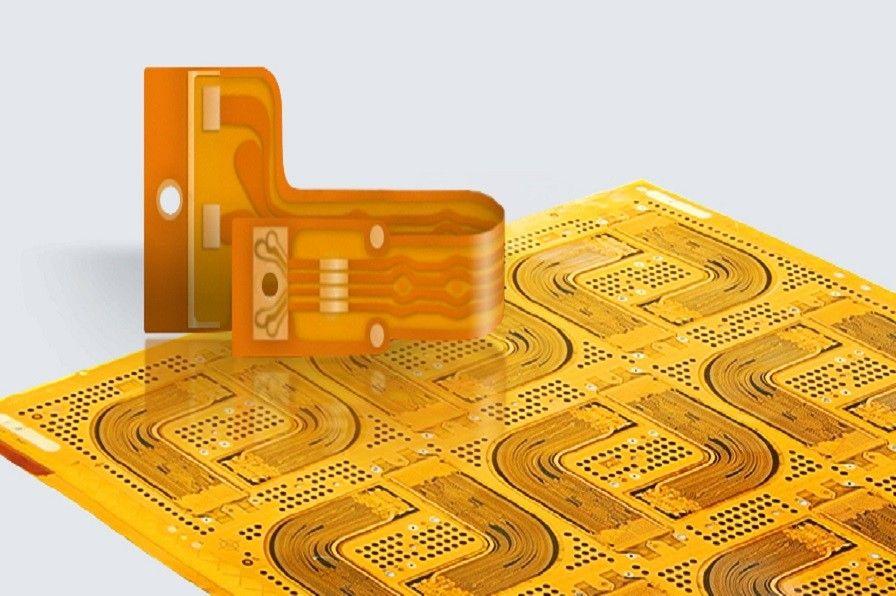
Flex PCB Board FAQ
What is a flexible circuit?
What materials are they made from?
How much do they weigh?
Are they as strong as rigid PCBs?
Are flexible circuits more expensive than rigid PCBs?
What are the advantages of using flex versus cables?
What are the preferred hole and pad sizes for flexible PCBs?
What are the best flex prepreg materials?
What are the alternative prepreg materials for joining flex and rigid materials?
What does a real stackup look like? (Not four signal layers, plane layers needed)
The plane layers for the flex are the same as the would be for the rigid board. This board would be turned into a 6 layer board, as follows:
Why aren’t you using coverlay?
Mask can be used as-submitted, without any additional considerations. This is ideal for customers used to typical pcb processes, and doesn’t require design or library changes to switch to a Flex pcb.
Coverlay requires a number of additional design considerations to avoid manufacturing issues. Since most of our customers do not have design tools that can check for coverlay-specific issues, it would generate a lot of surprising fabrication issues and/or silent changes. We’d prefer to avoid both of these.
What’s the minimum width of a flex strip?
What’s the minimum bend radius?
These table should help as a rough guideline to check your calculations. Due to the application specific nature of actual bending, we can make no warranty about correctness.
The bend radius depends on the board thickness of all layers passing through the bend. Multiplying the total thickness by the appropriate “bend ratio” then generates the expected bend radius. See our stackup for details on layer thicknesses. For simplicity, the following calculations include mask on both sides, and the number of copper layers listed.
A “static” bend is intended to be bent into shape and mounted, and is not intended to be bent from that point onward.
Copper Layers in bend | Conservative static bend | Agressive static bend |
---|---|---|
1 | 10:1 ratio, 74mil (1.8796mm) | 6:1 ratio, 44mil (1.1176mm) |
2 | 20:1 ratio, 216mil (5.4864mm) | 12:1 ratio, 130mil (3.302mm) |
A “dynamic” bend will have a bend/straighten cycle during normal operation. Estimating the “dynamic” bend radius is more complicated, and rough guidelines are harder to define. We recommend simply making dynamic bends as large as your application will allow to minimize wear. Sharper dynamic bends will result in decreasing the number of bends a PCB can survive prior to failure.
Copper Layers in bend | Agressive dynamic bend |
---|---|
1 | 10:1 ratio, 74mil (1.8796mm) |
2 | 20:1 ratio, 216mil (5.4864mm) |
Note, due to the use of soldermask instead of coverlay, our Flex PCBs are not well suited for use in applications where dynamic bends are used for operationally critical systems, such as medical and industrial.
Are there any design rules for placing parts on the flex circuit?
Are there recommended dimensions for the hatch pattern?
What is the most cost-effective type of via for HDI rigid-flex designs, stacked microvia or blind/buried vias?
What is the purpose of stiffeners?
- To strengthen any specific area of the board.
- To maintain proper thickness in the flex circuit.
- To support PCB components and connectors.
- To constrain the flexible parts to areas where they should be.
- To facilitate better handling of a thin flimsy circuit board.
- To keep certain areas of flexible circuits flat and stable.
- To meet ZIF connector specifications.
- To increase the bend radius of the circuit at the intersection of rigid and flex part. This will avoid the stress on flex part during multiple bending operations.
Basically, you use a stiffener when you require a rigid area in your flex circuit, maybe to protect components or connectors attached there. This will not let the circuit bend and protect the integrity of the part’s solder joint.
Continue reading our guide to PCB stiffeners.
What is the temperature that the rigid flex material usually supports?
Copper foil: adhesive or adhesiveless material.
Lead-free: not flame-retardant, has less outgassing (used in the military).
Do S curves in the flex region help with flexibility?
Where are dimension tolerances specified?
How many layers can your flex region have? Can you have hashed ground planes on either side of the signal layers for noise purposes?
The number of layers depends on the design requirements. 12 layers of flex is not unheard of; however, the higher the number of flex layers, the more difficult it is for the PCB to flex. Yes, you can have hashed ground planes on either side of the signal layers.