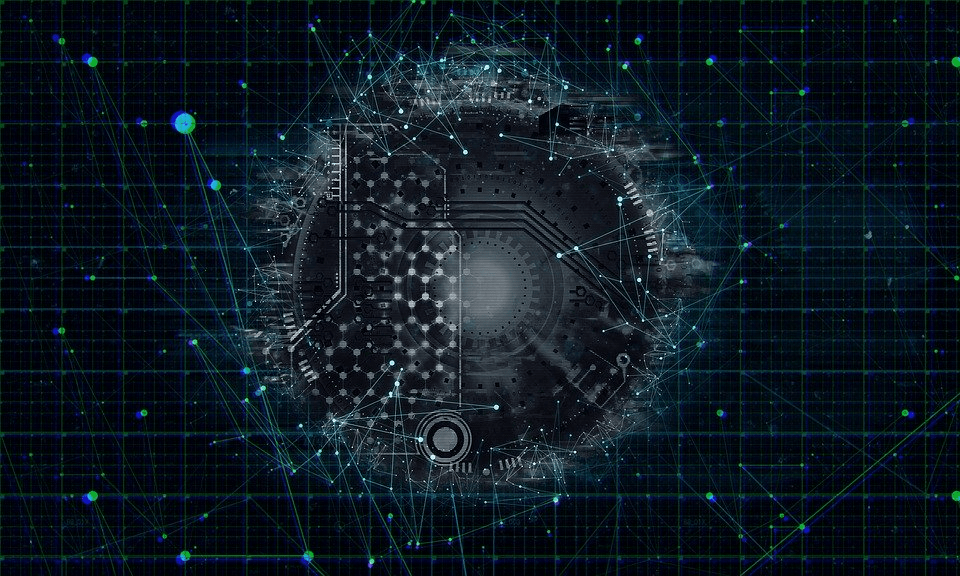
How a PCB is made
How Do You Make A PCB?
Printed Circuit Boards or PCBs have been around for ages. Despite being the electronic backbone of most devices, PCBs of the old days used to be inefficient and bulky, making the devices larger and heavier than they needed to be. But a lot has changed over the years. In pursuit of smaller and compact devices, PCBs shrunk in sizes and improved in functionality. The new flex and HDI PCBs aren't only a fraction of classic PCBs' dimensions and weight; they are far more durable and tolerant.
It's essential to understand how far along PCBs have come because just as it is with the circuit, the process of making them has also evolved. Simplest PCBs can still be made at home with a few simple tools, but for most complex PCBs, the process of making a PCB includes at least three different entities: The designer, fabricator, and assembler. Nowadays, most fabricators offer to assemble services as well.
Different PCB Makers and How Do They Make a PCB
Before you start thinking about making a PCB, the first choice you have to make is about what kind of PCB you will make. That would impact the materials you choose, the design consideration, and the final product's cost.
Choosing The Right Type of PCB
What you need the PCB for mostly determines the type of PCB you need. For specific products where size and weight aren't an issue, and you only need to pack a few components on the PCB, a Rigid PCB is an adequate choice. It's relatively simple to design, and if the circuit is basic, you can probably make it at home.
If you need a circuit that has to bend and flex, you need a Flex or Rigid-Flex circuit. A pure flex circuit is a bit difficult to design and costly to manufacture. But for wearables and some other applications, a flex with rigidized parts might be cheaper than a rigid-flex. For more durability and better component allocation and density, a rigid-flex would be a right choice. Another factor that comes into play here is whether you want the circuit to flex only a few times (static flex) or be regularly bent and flexed (dynamic flex). That’s almost impossible with a high number of layers.
Lastly, there is an HDI. It’s not mechanically different from other types because it's either flex or rigid PCB, but it can be more densely packed with components and have finer traces, thanks mostly to microvias.
Design Consideration
When you’ve decided on what kind of PCB you are going with, you have to choose to pick what software you will be using to design your PCB. It usually doesn't impact the manufacturing and assembling of the PCB, as long as your design outputs are in the right format. There are other important design considerations that you should know. You will start by designing the circuit. This will help you identify all the components and connections.
While designing the actual PCB, you have to focus on component placement and trace management. Small things like not knowing the component packaging size can ruin your design. Because even if it seems okay on the schematic (where you only leave place for its connectors), a component body (if it's bulky enough) can prevent other components from being placed in its vicinity. Component orientation is also an essential factor.
Even if a circuit is complicated, try working with a smaller number of layers. Too many layers mean more lamination cycles, and it adds to the cost. Speaking of cost, you should also consider the core material, laminate material, type of copper, and adhesive (if you are not using adhesive-less laminate). FR-4 is usually fine for most simple Rigid PCB circuits, but for high-speed circuits, you may need specialty materials from Megtron, Rogers, etc. Annealed copper offers more flexibility, but it's costlier than regular electrodeposited copper.
Then there are board and design constraints. Ideally, you should know which manufacturer you will be working with so that you can go through their design guidelines and don’t design a circuit that’s beyond their scope of capabilities.
Manufacturing/Making a PCB
Once the design is completed, it's sent to the manufacturer. The manufacturing or fabrication process is different depending upon the type of PCB it is (Rigid, flex, etc.), but there are some commonalities. Like most designs are first run through DFM (Design for Manufacturing) checks. These checks determine whether the design is feasible to fabricate (based on the technology and expertise available to the manufacturer). This prevents costly partial fabrications and saves time.
The design (inner layers first) is then printed on a special film and plotted over the substrate core. It’s than bathed in acid to scrap away the copper, not protected by the film covering. Then the film is removed to expose copper traces. Layer-only microvias are drilled. Further layers are printed and drilled in the same way. Then these layers are stacked and laminated together. The more layers there are, the more lamination cycles your PCB might have to go through, boosting the final cost.
Once all the layers are stacked together, PCB makers drill Plated-Through holes. The outer layer is protected, and silk screening is done to convey the necessary information. The board is tested to ensure all the connections are working.
Assembling
If there are no major problems in the design, the assembling process is usually a breeze. A pick-and-place machine takes care of populating the PCB with components. Some components that are either too big or don’t come under the purview of automatic assembling are placed and soldered manually. The PCB is tested again after assembly.
Conclusion
For most engineers, making a PCB is mostly just designing it, but they should be familiar with certain design and assembling practices. And they should especially look into the design guidelines provided by the manufacturer. This ensures successful PCB manufacturing and assembling. The PCB makers/ fabricators don't have to make any extensive changes in the PCB design (potentially altering its electrical characteristics) to make it suitable for manufacturing. Working with PCB makers who have extensive knowledge and expertise, and access to cutting-edge technologies is usually a good idea, even if you are working on a relatively simpler design. They can help you make a PCB that meets your requirements perfectly, at an optimal cost.