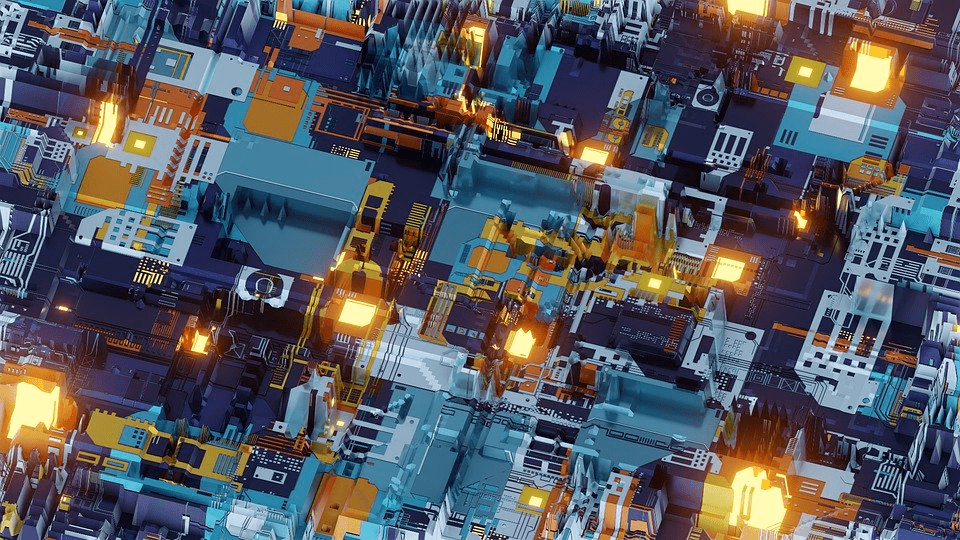
How is a PCB manufactured
How is A PCB Manufactured?
For electronic engineers and designers, the lion's share of creating a PCB is about the design. If a PCB is appropriately designed, manufacturing and assembling it will be easier. But if there are problems with the system itself, the PCB manufacturing process will be rife with issues.
While it's true, a problem that many designers face is inadequate exposure to the PCB manufacturing process. If they don't know what the manufacturing process is, the steps involved, how it has changed over the years, and how manufacturing capabilities differ from one fabricator to another, they may make costly design mistakes.
This is why it's essential to know about the PCB manufacturing process. It differs slightly for different types of PCBs (Rigid-Flex, Flex, and Rigid), but certain core methods are still the same.
Step-By-Step PCB Fabrication
If you look at the process of creating a PCB from a manufacturer's perspective, the priority will be to design something that sits neatly in the capabilities and expertise of the manufacturer. Most PCB fabricators don’t shy away from unconventional manufacturing requirements (Unless they are entirely out of the scope of their abilities), but fulfilling those requirements might cost additional time and money.
On the contrary, designers try to push the limit of their design. Whether it's the device requirement or the desire to seek maximum efficiency, designers try to achieve full functionality from the most compact circuits. Therefore, both the designer and the fabricator must start communicating before or halfway into the design process. Both of them should be on the same page regarding design requirements, manufacturing practices, and the finished product's cost-aspect.
The exact PCB fabrication process can be divided into several steps, but let's break it down into five significant steps for your simplicity.
DFM
The design of the manufacturing process is usually the first step in PCB manufacturing. The design is tested for feasibility and compared with the technical capabilities of the PCB manufacturer. If it passes, the design can be forwarded to the relevant department to start fabrication. But if it doesn't, the design is either corrected on-site, by engineers in the fabrication facility (since they know how it needs to be adjusted to fit their fabrication protocols.
The designer is also brought into the loop because they need to ensure that the changes in design warranted after the DFM process do not affect the resulting circuit's electrical characteristics. The DFM process helps eliminate costly remakes and reprocessing of the circuit and saves a lot of costs.
Traces
The next important part is creating copper traces. The first layers that are worked on are usually the innermost layers: The core/substrate. The copper patterns of the innermost layer (for both sides of the core) are printed out on a particular photographic film. The copper is either deposited on the core's innermost layers using the Electrodepositing method (cheaper, but not very flexible, making it harmful for flex PCBs), or annealed copper.
The patterns are then printed over the copper layer, typically using UV light. Then, the copper-plated core/PCB board is dipped in a solution to get rid of the copper not protected under the film. Once the traces are set (still hidden under the film/ink), the ink is removed by dipping the board in another solution, revealing the copper underneath. This is how all the layers are traced, except for the outermost ones. The tracing process is usually reversed for that.
Drilling
Drilling, especially laser drilling to create micro-vias, is done layer by layer. For the core, where a singular layer contains both a top and a bottom layer, it is drilled differently from the subsequent layers where one layer only has one surface (and the bottom is fused with the top of the layer beneath). Once all individual layers are drilled, and micro-vias are lined up to create stacked or staggered connections, the layers are fused, the plated through holes are drilled.
The drilling is very different from Rigid to Flex. There are even more considerations when it comes to FlexFlex. When it comes to flex circuits, you can’t drill in (or near) the areas where the PCB has to Flex; that's especially true for plated through holes that go many layers deep. The reason is that the conductive plating of the plated through hole might get fractured when the circuit flexes.
Lamination
Laminating the PCB layers is the process of fusing all the individual layers/sections of PCB. It's also one of the significant cost drivers. A simple rule of thumb here is that the less circuit's lamination cycles, the lower the cost will be. So it can help if you never tried to overcomplicate your PCBs by adding layers upon layers.
The plated-through-holes that go from the top to bottom surface are drilled and plated after the lamination. The process also differs if you use the adhesive-less laminate for different layers or an adhesive between different layers. It also impacts the final cost.
Assembling and Testing
The assembling of the final circuit is done after the board is all set and ready. The final laminated board is tested for the connectivity of the traces. For specific high-speed applications, the board may also be tested for signal integrity and noise at high frequencies. Once the board is tested, it’s assembled (populated by components) on both sides. For bulk assembly, a pick-and-place machine is used. For prototypes, manually assembling the circuit can be cheaper.
The final circuit is also tested, with all the components in place. Solder masks are applied, and silkscreen is placed to convey important information about the PCB.
Conclusion
If you are creating an HDI PCB, a Flex, or a Rigid-Flex PCB, the manufacturing process can include a few more steps. For example, a dynamic flex may be subjected to multiple flex cycles (usually in the thousands) after the PCB is finished. This is done to test the integrity of the traces, vias, and components. Other considerations may include choosing specialized materials to ensure specific electrical characteristics or accommodate the circuit's mechanical requirements. Working with PCB fabricators that have access to cutting-edge technology and employing the best-in-line techniques can save you a lot of costs and ensure that the circuit is manufactured to near perfection.