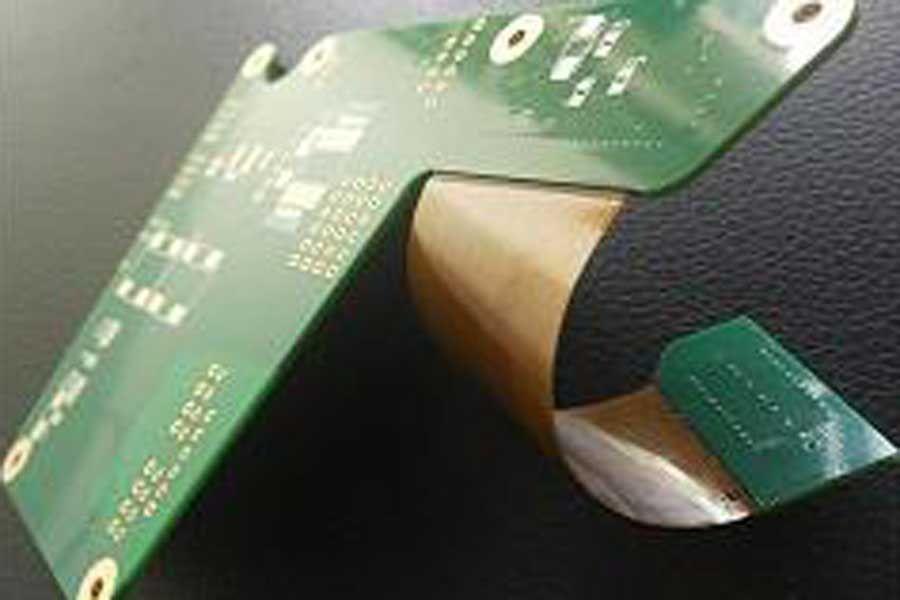
What is HDI rigid-flex
Circuits boards are essential parts of any electronic system. They provide electronic product manufacturers a platform to integrate various electronic components to power up electronics products. The size of such boards often determines the number of components that will be needed to achieve optimized electrical functions.
In a bid to economize circuit board size and optimize electrical functions, PCB technology is taking a toll on several companies' production line. As PCB technology keeps evolving, professionals keep upgrading the printed circuit board they utilize for their PCB ASSEMBLY.
Two most commonly used circuit boards by many of these companies include :
- Rigid circuit board
- Flexible circuit board
RIGID CIRCUIT BOARD
Rigid PCB is a kind of regular PCB which can neither be folded or twisted into any shape. This is often accompanied by FR4 stiffener which increases the amount of a board stiffness and rigidity. It’s typically composed of copper trances and paths. These elements are much incorporated onto a single board so as to connect them with various kinds of board components. In most cases, the base material of the board is created with a rigid substrate that offers rigidity and strength to the board. A typical example of rigid PCB is a computer motherboard. It comes with the rigid substrate material. They are however cheap as compared to flexible PCBs. They are traditional forms of PCBs and widely used in many electronics products.
FLEXIBLE CIRCUIT BOARDS
Flexible circuits boards are quite good for medical devices, sensors, implants and also mobile consumers. Their relevancy emanates from their ability to fit into any limited space. Specifically, they suit products which need:
- Lightweights
- Short and vibration resistance
- The low number of device interconnects
- Three- dimensional packaging geometry
- Miniaturized versions of existing technologies
The idealness for high temperatures and high-density applications are other strong reasons to use them.
The flexible substrates are much configured to exist in a frequent state of flex. They are usually created into the flexed curve during their installation.
Flexible circuits are often divided into two major types, they are
- Static flexible circuits
- Dynamic flexible circuits
While the static flexible circuits are known for undergoing minimal flexing during assembly and service, the dynamic ones are noted for frequent flexing. These dynamic flex are often found on printer head, disk drive head and around the hinge on a laptop screen.
NEWER PCB TECHNOLOGY: WHAT IS IT?
The evolution regarding PCB technology doesn’t end with those two circuit boards. Because there is a need for small-sized devices performing great functions, printed circuit board production companies stepped up to rigid-flex PCB manufacturing.
What is Rigid-Flex PCB?
Rigid-flex printed circuit boards are boards that utilize the mixture of both rigid and flexible board technologies in a certain application. They are often characterized by multiple layers that have flexible circuit substrates. Those layers are often attached to two or more rigid boards externally or internally depending upon the design of an application. The two in one circuit – RLC has with one another through the plated thru-holes.
The designs of rigid-flex are much time consuming and tasking than engaging in the design of certain rigid board environment. This is because these boards are mostly designed within a 3D space. Thus, they produce higher spatial efficiency. Through such design, it’s much possible to roll, twist or fold them to accomplish the desired shape for the final application package.
The rigid-flex board is much common in smart devices, cell phones, and digital cameras. They’ve also been fabricated for use in the medical world. The same reasons for using this Rigid-Flex Circuit in the medical and camera world applies to its use in designing smart control systems. Rigid-flex circuits are also been adopted in both aerospace and military industries for over 2 decades.
Rigid-flex PCB is a complex product that often requires much communication between the customers and the PCB provider. When they are designed into consumer products, rigid-flex is not there for space or weight maximization. Rather, manufacturers included them to eliminate diverse needs to solder joints and delicate wiring. Often times, delicate wiring is prone to connection issues. So, this flex is placed to avoid any kind of connection issue. The rigid-flex PCBs are much efficient for almost all electrical applications.
During the Rigid-Flex PCBs design process, certain considerations must be taken into account for final product size variations. In the manufacturing of Rigid-Flex boards, the flexible polyimide core will shrink once the bonded copper foil is etched away. This variation must be accounted for in the design process. They can be used in testing facilities, and automobiles.
Their circuitry contains Multiple flexible inner layers. These layers are mostly attached together through the use of a bonding film. They often incorporate a board externally or internally to accomplish the relevant designs. Also, they can be combined to achieve the desired result.
Benefits of Rigid-Flex PCBs
- Space minimization through the deployment of 3D tactics
- Reduced board size and system weight.
- A lower number of device parts
- There is a higher reliance on connectivity as the number of solder joints is minimized.
- They are easier to handle during the assembly session.
- The assembly processes are much simplified.
- The integrated ZIF contacts help in providing simple modular interfaces to the system environment.
- They help simplify testing conditions. An advantage of the Rigid-flex circuit lies in its ability to offer the higher component density and greater quality control.
- Rigid-flex PCB manufacturing is a good way to minimize logistical and assembly costs.
- A rigid-flex circuit is useful for increasing the complexity of mechanical designs. As a result, they help improve the degree of freedom for optimized housing solutions.
The distinction between both circuits lies in the construction methodology and material selection. There is a number of layer stack-up configurations that can be fabricated as rigid-flex, each with their own electrical, physical and cost advantages.
Perhaps you need to further information about HDI rigid-flex, don’t hesitate to contact Hemeixin at This email address is being protected from spambots. You need JavaScript enabled to view it.. Do you need to know the market price for the product? Get a quote here: https://pcbonline.hemeixinpcb.com/