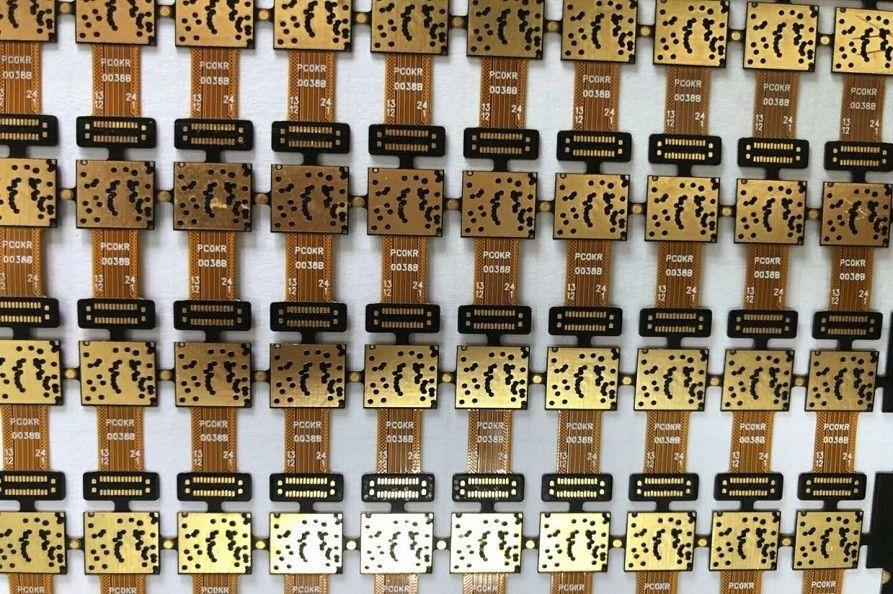
Price Considerations for Flexible Circuit Design
Flex circuit are becoming increasingly popular. They are light, mechanically flexible, and allows for 3D designing. This makes up for the design complexity and price considerations they come with. But understanding the factors that drive the cost of a flex circuit may help you control it.
Flex Circuit Design Price Consideration
One of the general rules of thumb regarding price considerations is that whenever you go overboard the conventional design rule and fabrication norms, you are going to add to the cost of the circuit. This is something most designers understand, but the continuous need to innovate, especially for designers who primarily make prototype circuits, usually require unconventional designs. And for flex, even some conventional elements can add to the cost. Some design factors add less to the cost than others.
Most flex circuit Significant Price Considerations
Some of the highest price/cost drivers are:
Layer Count: Layer count adds most to the price of a flex. A higher number of layers add to the complexity of the circuit by default, since it requires multiple lamination cycles. Since a flex circuit can be designed and installed in 3D, it’s smarter to use more surface area for a higher component density instead of adding the number of layers and, consequently, increasing the cost. From a comparative analysis, it's seen that sometimes dividing a flex with a higher layer count into two flex circuits with lower layer counts is more cost-effective.
Another thing that happens in relatively more complex circuits is dissimilar layer count in the areas where you need plated through-holes drilled in your flex. That is also a major price consideration, and keeping a uniform number of layers throughout the flex is usually a good idea to keep costs relatively low and give the circuit better mechanical stability.
Advanced Technologies: Whenever you go beyond the fabricator's traditional guidelines or require something in the circuit that will need the fabricator to change the assembly line, it will add to the cost. Things like requiring a trace width/space smaller than four mils (for some cutting edge fabricator, that’s down to 2 mils), or requiring hole size below ten mils (6 mils for some fabricators). This is one of the major reasons why working with fabricators who employ state of the art technology can help you bring your bottom line costing down.
Buried Vias: Buried vias provide an amazing layer to layer connectivity, and they help enhance the electrical capabilities of the circuit. But they are also a major price consideration when designing the flex. Unless you are working with stringent electrical requirements or on the high-speed circuit where noise can be a major issue, avoiding or minimizing the use of buried vias can help you keep a better handle on cost.
Material utilization: It’s one of the choices you have to make in the earliest stages of designing the flex. A lot of different materials are used, some for their superior mechanical and thermal stability, and some for better electrical characteristics. The choice for the conductor is usually always copper, but the substrate and adhesives may vary. Three common adhesive and substrate combinations that are prevalent in the industry are PI (polyimide) with acrylic adhesive, PI with flame retardant adhesive and adhesive-less PI. The first one is most commonly used in lower layer counts, whereas the last one is mostly preferred for high layer counts on account of its better CTE. It's relatively more expensive and one of the cost drivers of high-layer count flex PCBs.
ZIF Connectors or Buried Access: It’s becoming a common replacement for wire and connector based assembly, especially in circuits where we have to marry flex with rigid circuits. But the need for buried access comes with a higher cost.
Selective Plating for Outer Layers: Some circuits may require the need to use two different copper weights on the same layer. This selective plating usually ends up driving the overall price of the PCB high.
Panel Utilization: How cleverly you can use the panel space of the fabricator can impact the cost. This is viable only for multiple pieces of a large single flex circuit, or if you are getting several flex circuits fabricated. More flex areas you can get on the same panel size, the better. Let's say if you are working with a fabricator who offers the panel size 20" by 80", and you can get ten flex circuits on it by changing the design, where you were originally only getting six, you can significantly reduce the price.
Other flex circuit Price Considerations
There are other factors that contribute to the price of the flex circuit as well. They may not add too substantially to the cost, but they are still factors to consider.
Controlled Impedance: This requirement of the flex circuit usually adds to the design complexity and to the price.
Line Width/space: The bottom threshold size isn’t the only price driver. The smaller the drill size you require, the more you may have to pay for it.
Stiffeners: Many flex circuits used stiffeners to anchor the components. This makes them a makeshift and cost-effective replacement for pure rigid-flex circuits. The use of stiffeners complicates the circuit assembly, and trace continuity is disturbed. Stiffener material is also an issue. Typically, FR-4 materials cost the least. Other materials may hike the price.
Drill Hole Count: This is usually a factor with mechanical holes. Since more holes mean a higher tooling cost, usually greater than 30,000 is a problem, but it varies from fabricator to fabricator.
Button Plating: Selectively electroplating copper in the vias and onto the via capture pads is also a price consideration.
Added Tear Stops: While it’s a good design practice to add tear stops to the flex areas where a sharp turn might allow the flex to tear if there is any undue strain on the circuit. But tear stops can be a bit pricy.
Annular Rings: Annular requires extra precision and careful fabrication, especially in the flex circuits.
Edge routing, some strain relief methods, and complex routing are also price considerations.
Conclusion
Many of the price considerations and cost drivers are being taken care of as flex circuits become more and more commonplace. Many of the factors driving the cost may be vendor-centric. So if you are working with a fabricator that has years of experience and cutting-edge flex circuit fabrication technologies, they may be able to help you get around the price considerations and cost-driving factors.