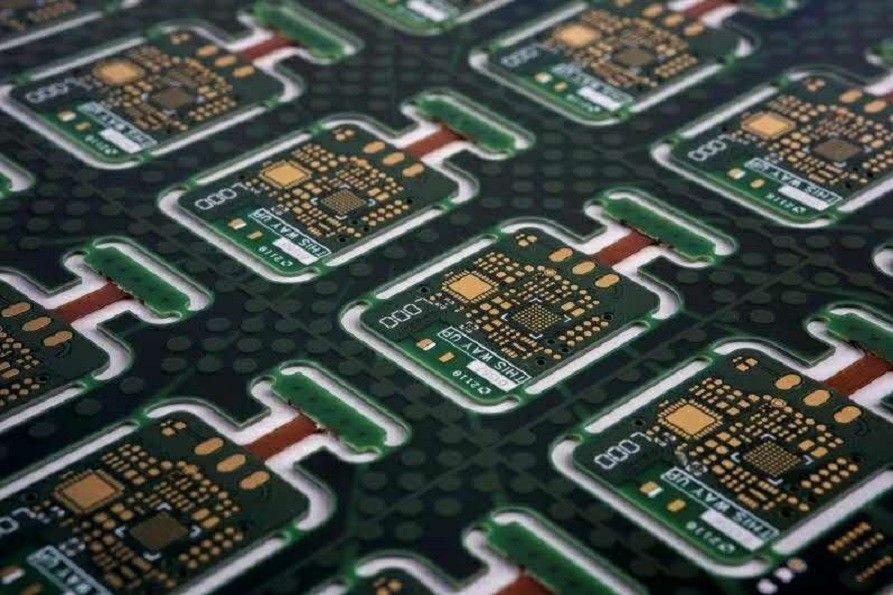
What is A Rigid-Flex PCB?
Conventionally, PCBs were nothing more than hard boards with holes to anchor and sold components. These were the forefathers of what we now call a rigid PCB. Now, circuits have gotten way more complicated, dense, durable, and flexible. Owing to the compactness and high-quality circuitry needs of the market. And one of the best things to happen to the circuit technology is the creation of rigid-flex pcb.
What is a Rigid-Flex PCB?
A rigid-flex circuit combines the features of both rigid PCBs and flexible PCBs. The circuit is part rigid, (mostly for component mounting), and part flex (mostly for interconnection). This combo allows engineers to design the circuit in three dimensions. And it also allows for an easier component mounting than a pure flex circuit does.
In a rigid-flex circuit, the substrates for both rigid and flex PCBs are fused/laminated together. In most multilayer rigid-flex, the flex substrate is usually sandwiched between the rigid substrate layers. This offers much more mechanical stability than either rigidized flex or separate rigid circuits connected by wires' offer.
Key Features and Differences of Rigid-Flex PCB
It’s easily understandable that rigid-flex circuits are significantly different, and in most cases, better than the rigid and flex circuits. But going through the differences, distinct features, benefits, and shortcomings of rigid-flex circuits might offer you a better understanding of the true potential and limitations of a rigid-flex circuit.
1. Unlike rigid circuits that are designed with minimal mechanical considerations, a rigid-flex is created by keeping in mind the harmony of the mechanical and electrical side of the circuit. In this regard, it’s very similar to the flex circuits. Designing a rigid-flex is just as much a mechanical process as it’s an electrical one.
2. One of the major limitations of pure flex circuits is component placement. In a flex circuit, you can't place the components or vias anywhere you like. You have to keep in mind the bend radius as well as the static or dynamic quality of the circuit. In some cases, this limitation is overcome by rigidizing the circuit (by hardening some areas of the flex to make them rigid for proper component anchoring). But that, in turn, creates issues with the proper trace routing. A rigid-flex, on the other hand, is very "component friendly" in this regard. If you are designing a rigid-flex with maximum component density on the rigid area of the circuit and minimal usage of flex real estate, you won’t have to worry about component placement. Or fractures in the plated vias in the flex part of the circuit.
3. A rigid-flex is usually divided into three zones: rigid, flex, and flex transition zones. Transitions zones are areas where the flex meets the rigid part of the circuit. Special care needs to be taken for the transition areas because any undue movement there can cause fractures in the copper lines. For mechanical stability, the flex coverlay is extended a little over the rigid area.
4. Rigid-flex boards usually combine single or multiple layers of flex with rigid PCBs. For low layer counts, especially for a lower number of rigid layers, the flex substrate is usually laminated on top of the rigid layers.
5. Rigid-flex PCBs offer more design flexibility due to the three-dimensional nature of the design. And by reducing the need for wires and connectors, rigid-flex circuits are also relatively lighter, increasing their mechanical durability against jerks and vibrations. This is one of the reasons why rigid-flex circuits are so popular in applications that work in harsh environmental conditions. Also, the lack of connectors means fewer solder joints and potentially fewer failure points in the circuit.
6. Since typical multilayer rigid-flex circuits are built around the flex substrates, the circuits are usually very thin. This allows the circuits to be used in weight-sensitive applications, and improve the overall reliability.
7. One major limitation of the rigid-flex PCB is its cost. A rigid-flex circuit is usually much more expensive than a simple rigid, or even a rigidized flex circuit. Especially if you are only getting a few units fabricated, like for a prototype. But as the number of units increases, there are many ways to control the cost of a rigid-flex circuit. The extra cost is simply due to the complexity of fabrication. Combining flex and rigid circuits together requires multiple lamination cycles, more lamination cycles means more cost. Another major cost driver is the material. No-flow and low-flow prepregs used in the construction of a rigid-flex cost five to ten times more than the conventional substrate materials.
8. Another drawback of rigid-flex is the design complexity, especially for the first time designers who aren’t well-versed in working with flex. It’s imperative that the designers who are working on rigid-flex for the first time to go through the established design practices and follow the guidelines of their fabricators.
9. Some common applications of rigid-flex PCBs are devices that need to operate in a harsh environment. Rigid-flex circuits are mechanically and thermally much more stable than flex circuits. It can replace the lightweight flex circuits in places where the device containing the circuit is exposed to harsh environmental conditions while maintaining and even enhancing the electrical characteristics of the circuit. Another area where rigid-flex circuits are preferred over other circuits is where reliability trumps the cost of circuit fabrication. In some high-density packaging needs, rigid-flex circuits also fare much better than conventional rigid and flex constructions. Where four or more rigid circuits need to work in conjunction, replacing the separate units with a rigid-flex construction usually proves more cost-effective and reliable.
Conclusion
Despite its clear superiority, the use of rigid-flex is still not as commonplace as its capabilities and benefits warrant. Still, there are places where you have to use a rigid-flex circuit, no matter the cost. And while the cost is an issue, it's not an insurmountable barrier. You can significantly reduce the cost of your first rigid-flex circuit by following good design practices, choosing your materials wisely, and designing with the fabricator's capabilities in mind. The smart idea is to loop in the fabricator in the design stages, so they may guide you and prevent you from making any costly mistakes with your rigid-flex PCB.