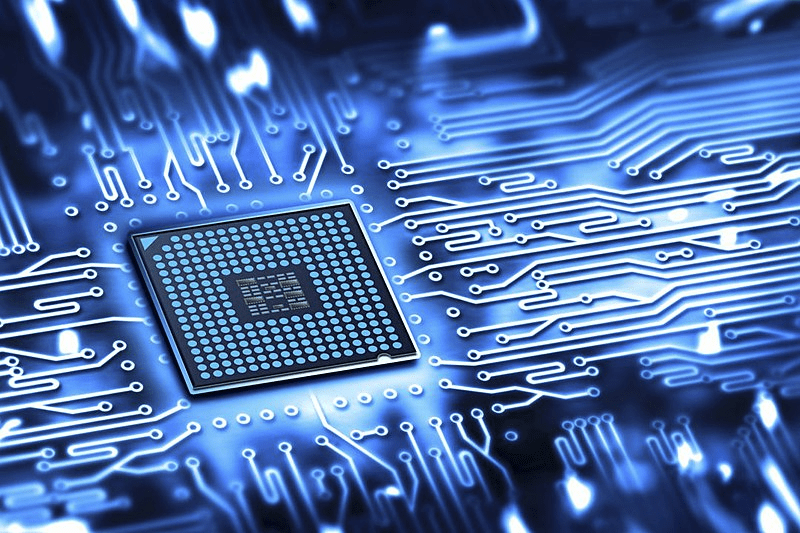
HDI DFM Process – What is it, and how it helps?
Perfecting The HDI PCB DFM Process
HDI PCB are now at the forefront of electronic innovations and the core of many sophisticated and compact devices. Many devices, like new 4G and 5G smartphones, drones, digital cameras, many wearables, and complex military devices like smart ammunition and missile systems, all have HDI circuits as their electronic backbone. The ability to pack a lot of circuitry on a small chip isn’t the only virtue that HDI circuits have. Many HDI circuits offer significantly higher functionality (like less noise at high frequencies), without using specialized materials. Also, HDI circuits fare much better in harsh environments than most conventional circuits do, making them ideal for applications like space probes and military gadgets.
HDI circuits are sophisticated, and they require special care and consideration in design, manufacturing, and assembly. HDI PCB designers must be very ingenious with real estate available for components on the PCB surface, traces, microvia placement, and stacking. Overly complicating an HDI circuit can drive the cost up. Therefore HDI designers and PCB manufacturers must start communicating as early as possible, so there is no confusion regarding manufacturer guidelines or cost implications of multiple lamination cycles.
One of the most important stages in an HDI PCB’s lifecycle is DFM – Design For Manufacturing.
The HDI PCB DFM Process
DFM or Design For Manufacturing is the process in which your PCB manufacturer, who has the designs for your HDI PCB, review that design, and compare it to their manufacturing and assembling capabilities and process. The concept is simple, instead of starting on a design piece by piece and running into a problem midway when half the PCB is manufactured. Even worse, the PCB fails at the testing stage, and you don't know whether it was a fault in the design or a manufacturing flaw, the manufacturer runs a DFM check.
The check reveals whether the design you've to send them is something they can manufacture and assemble, and it's per their design guidelines or not. If it is, then simply by running this check, the PCB fabricator can save themselves and the designer a lot of time and effort.
If the check reveals issues with the design that will cause problems later in the PCB fabrication stages, they usually contact the designer. If the designer consents, the engineering team can either work out some of the kinks themselves, send the design back with their feedback, ask the designer to make necessary changes, and ensure that the design now complies with PCB manufacturing capabilities the fabricator.
Perfecting the HDI PCB DFM Process
The HDI PCB DFM process has been improved over the years. It can also be used to improve your PCB design. Understand different elements of the DFM can help manufacturers gain a better understanding process and how it benefits them.
- Even if there isn’t an issue with the design, the fabricator can still contact the designer after DFM with their feedback and suggestions. Based on those suggestions, if the designer can improve their HDI design (as long as it complies with fabricator guidelines), they can potentially improve its performance, yield, PCB design throughput, and lower the cost.
- DFM can also help designers and fabricators together use the Continuous Design Improvement Model. This helps all involved entities to understand each other’s goals and can work better together. For example, the designer wants a circuit that gets the best output/performance for the least possible cost. The manufacturer wants something that’s not just within their purview and capabilities, but well within it so that it's easy to fabricate. Similarly, the assembler wants component placement pre-tested to ensure that the proposed components aren't too big for the real estate available on the HDI board. The DFM helps keep all three on the same page.
- DFM can also help ease the design complication of HDI PCBs. By differentiating what the designer wants and what they need, fabricators can ask designers to rework on the design and remove unnecessary add-ons. It doesn't just reduce the overall cost and manufacturing complications but also make the PCB perform better.
- To help make the DFM process go through as smoothly as possible, the designer should provide all the necessary files in the correct format so that the fabricator can run the design through their DFM steps without any complication. If the designer is reluctant to share the complete design, it might cause issues in the DFM, and consequently, the HDI PCB fabrication process.
- Checking for part availability is also part of the DFM process, so the designer should keep an open mind about potential replacements. Or, they should be willing to wait for the exact component to be shipped and ready to bear the additional cost. This is more of a problem with HDI circuits because thanks to design complications and performance requirements, there is usually little room for swapping one component for another.
- DFM also checks for potential performance issues, and the fabricator may ask for the design to be updated for better materials and alternative layer stackups to improve impedance controlled routing. Component placement and trace routing is checked for signal integrity issues, especially in high-speed, high-frequency HDI circuits.
- DFM tests also include checking for component placement issues, which can cause problems in assembly. Component location and rotation check ensure that larger parts that are soldered before smaller components don’t compromise their joint quality. Pad size for chip components is checked for potential "tombstoning" problems. Acute angled traces can become acid traps (because they are hard to clean off after the etching process), and they are singled out during the DFM checks. Checking for testability is another important part of the DFM process.
Conclusion
While it’s true that DFM falls under the purview of the fabricator, it doesn't mean that designers can get away with a plethora of mistakes, thinking they would be caught and fixed during the DFM process. A designer should always consult the fabricator, as early in the design process as possible, and do their best to follow the design guidelines provided by the fabricator. The DFM process might help designers and fabricators "fix" a bad design, but it can't improve upon it. But if the design is efficient and clean to begin with, the DFM HDI PCB process can help designers and fabricators find multiple ways to improve it. For that to happen, you have to ensure that you are working with the right fabricator.